In the world of supply chain management, warehousing has often been overlooked overshadowed by the more “exciting” realms of manufacturing and planning. Yet, as many CEOs, Country Leaders, and Heads of Sales experience too often, things going wrong in the warehouse can drag a company into a dilemma of inefficiency and client dissatisfaction. Does the following scenario resonate with you… a key client hasn’t received their shipment and it’s YOUR phone ringing off the hook. Your Customer Service reports the goods are at the warehouse but mysteriously “unavailable for picking” in your systems – a classic scenario that’s frustratingly common. This isn’t just about a delayed shipment; it’s a symptom of recurring systemic issues often neglected in the warehouse, the heart of your supply chain operations. – We already highlighted the impact of poor Inbound management earlier in this article.
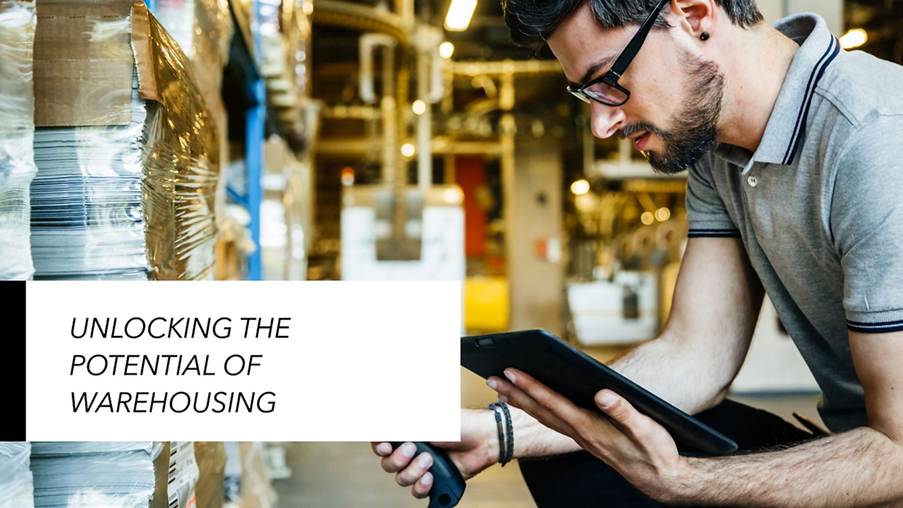
Our extensive work with over 100 warehouses in the last few years has proven that optimising warehousing practices isn’t just about cleaning up a messy corner of the business; it’s a strategic lever to pull for substantial gains. By implementing better practices for our clients, we’ve seen them enhance Customer Service Levels and also slash warehouse costs by 15-25% and overall supply chain logistics costs by over 30%.
Our experiences reveal recurring process challenges across various warehouses. These range from inefficient inbound processes with missing barcodes and manual delays to the misuse of premium warehouse real estate, like shipping gates clogged with pending returns rather than having space to pre-stage outgoing shipments and smoothen the workload in your warehouse at the same time.
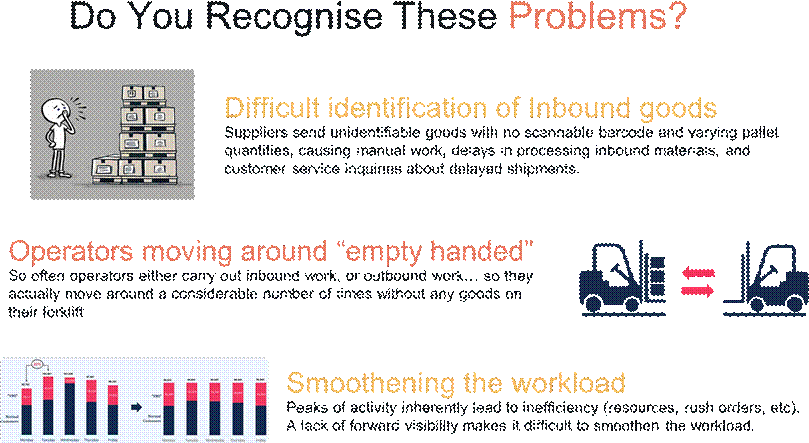
Empowering 3PLs: Breaking the Cycle of Cost-Centric Selection
3PL providers perceive client-imposed process requirements as a given. The price is generally perceived as the sole selection criterion. The “catch-22” in this dynamic, is that client companies actually expect the 3PL to bring the best-practice processes…
Having assisted many companies in their 3PL selection process, we noticed that the 3PL companies often do not dare to educate their client on what would make the warehousing more effective and how it could benefit the wider business (cost and service).
When there are warehouse challenges, we commonly see clients sending their logistics people into the 3PL “to try to solve the problem”, whereas the 3PL, (as a warehousing expert), should be the one feeling empowered to take their client through the end-to-end process and recommend changes to improve/resolve the situation.
The Hidden Costs of Neglected Warehousing
One might argue that upgrading warehouse processes is a costly affair that offers minimal return on investment. This couldn’t be further from the truth.
Consider this: a flawed inbound process might seem like a minor hiccup, costing “just a few thousand bucks” in labour savings. However, as these inefficiencies directly lead to back orders and/or rush orders, they balloon into substantial costs including additional warehousing, trucking, and even lost customers due to poor service.
It’s not just about the immediate savings – it’s about the ripple effect across your entire supply chain.
Why Warehouse Optimisation is Not Just a Nice-to-Have
Despite the clear benefits, consultants often disregard warehousing optimisation in favour of topics like lean manufacturing, network modelling or integrated business planning. Warehousing is not seen as a priority, and you’ll rarely find a consultant enthusiastically running through a warehouse with a hi-vis jacket inspecting every move!
A warehouse is considered a room where things go in and magically come back out, it is not seen as an area to find big savings. However, when the magic of the warehouse fails, it doesn’t just cause operational headaches – it impacts the entire business ecosystem.
Following significant output issues in their primary warehouse, a COO client told us: “I have been in Supply Chain for 25 years, but I never realised warehousing is actually a science”.
We advocate for recognising the warehouse as a critical asset in the supply chain, not just a storage room where boxes are moved around. By addressing the ten most common warehousing inefficiencies we’ve identified, companies can transform their warehouses into strategic assets that drive efficiency and customer satisfaction.
In conclusion, it’s time to give warehousing the attention it deserves. Adopting best practices in warehouse management can result in substantial business advantages. So let’s get to work and transform the often neglected part of supply chain management into its driving force.
0 Comments